Tesla's New Low Voltage Connector Standard (LVCS): A Game Changer or an Industry Challenge?
Tesla’s announcement of its Low Voltage Connector Standard (LVCS) has sparked considerable industry attention. While Vice President Tao Lin officially disclosed it on December 5th, Tesla had already provided detailed information about it on its website back in October. The LVCS aligns with the shift to a 48V system, driven primarily by the needs of Tesla’s Cybertruck, and Tesla is advocating for industry-wide adoption. However, achieving standardization in vehicle connectors—particularly for low-voltage (LV) systems—remains a complex challenge.
From an automotive industry perspective, unifying high-voltage (HV) and LV connector interfaces within vehicles is immensely difficult. Attempts to standardize LV connectors date back to the internal combustion engine era, with automakers such as Ford, GM, Toyota, Honda, Volkswagen, and BMW leading initiatives. However, these efforts typically resulted in a plethora of industry and corporate standards rather than a “winner-takes-all” solution. This issue isn’t confined to a few automakers; it’s deeply rooted in the entire supply chain.
To put this into context, a modern vehicle typically requires over 200 different types of connectors, divided broadly into power and data categories. In the era of electric vehicles (EVs), power connectors are further divided into HV and LV camps. Tesla’s LVCS focuses on the LV camp, which is critical for power delivery and signal transmission. LV connectors are also a key driver behind the density of a vehicle’s low-voltage wiring harness, an area notoriously difficult to automate. While processes like wire stripping and crimping have seen automation advancements, connector pre-assembly remains heavily reliant on manual labor, contributing significantly to costs.
So, why is it so hard to standardize LV connectors despite their low technical complexity? Let’s explore some key challenges:
The global variability in regulations further complicates the issue. For example, differences in charging interface standards across regions demonstrate how challenging achieving universal compliance can be.
In the EV era, leading connector suppliers have leveraged their early industry foothold to maintain dominance. While connectors are seemingly small components, they are deeply intertwined with industrial power plays, reflecting the challenges of transitioning to a fully localized or standardized supply chain.
The clock is ticking, and the stakes are high. Tesla’s LVCS is a bold step toward reshaping the industry’s approach to connector standardization. Yet, whether it will become the de facto standard or simply add another layer to the fragmented landscape depends on the industry’s ability to collaborate and innovate.
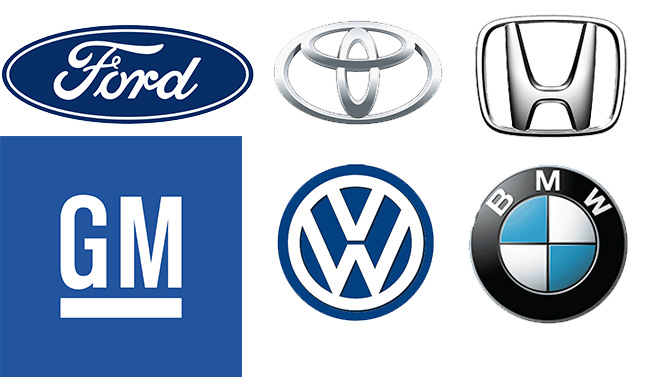
From an automotive industry perspective, unifying high-voltage (HV) and LV connector interfaces within vehicles is immensely difficult. Attempts to standardize LV connectors date back to the internal combustion engine era, with automakers such as Ford, GM, Toyota, Honda, Volkswagen, and BMW leading initiatives. However, these efforts typically resulted in a plethora of industry and corporate standards rather than a “winner-takes-all” solution. This issue isn’t confined to a few automakers; it’s deeply rooted in the entire supply chain.
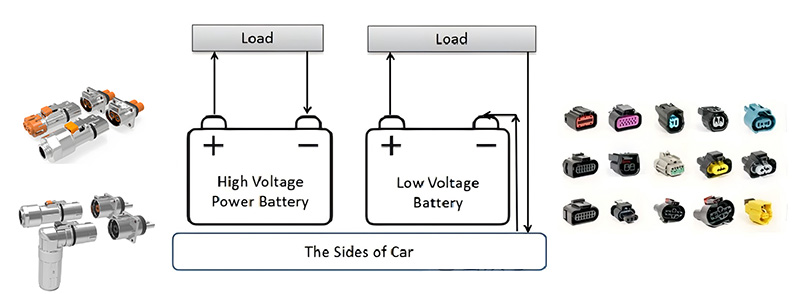
To put this into context, a modern vehicle typically requires over 200 different types of connectors, divided broadly into power and data categories. In the era of electric vehicles (EVs), power connectors are further divided into HV and LV camps. Tesla’s LVCS focuses on the LV camp, which is critical for power delivery and signal transmission. LV connectors are also a key driver behind the density of a vehicle’s low-voltage wiring harness, an area notoriously difficult to automate. While processes like wire stripping and crimping have seen automation advancements, connector pre-assembly remains heavily reliant on manual labor, contributing significantly to costs.
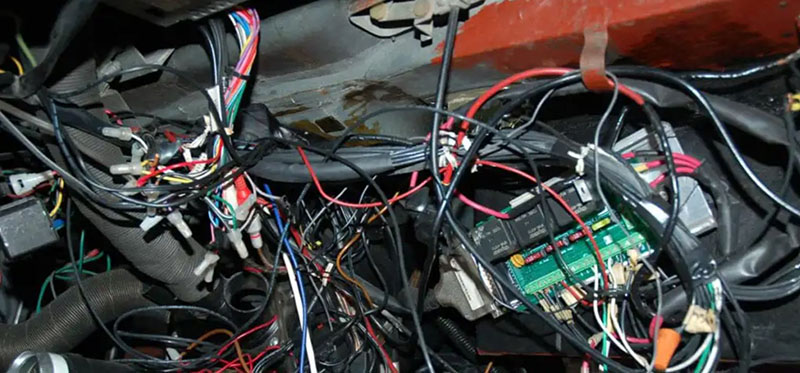
So, why is it so hard to standardize LV connectors despite their low technical complexity? Let’s explore some key challenges:
1. Supply Chain Complexities
Standardizing connector interfaces across vehicles disrupts existing supplier relationships. Most components on a vehicle are sourced from multiple suppliers to ensure cost competitiveness and supply chain security. If connector interfaces are standardized for interoperability, it’s ideal from a cost perspective. However, connector suppliers are often reluctant to provide cross-compatible warranties due to potential electrical issues and liability concerns. Even though there are no insurmountable technical barriers to interoperability, defining responsibility for failures is a significant challenge. This self-protection behavior reinforces supplier differentiation and hinders progress unless mandated by strong government regulations or certifications.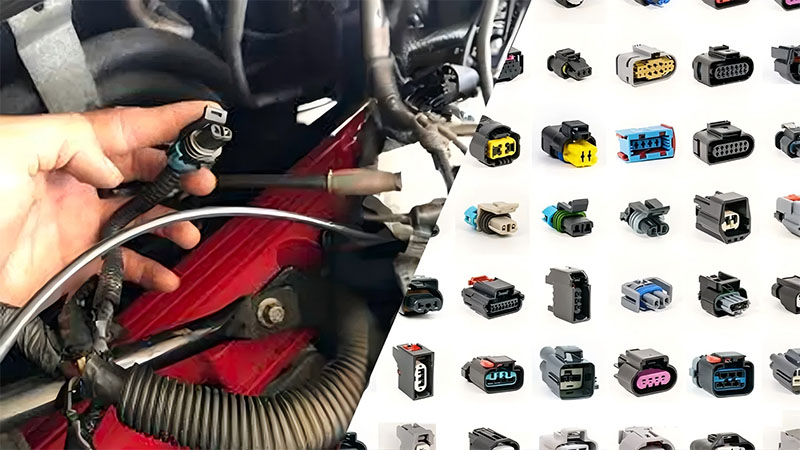
The global variability in regulations further complicates the issue. For example, differences in charging interface standards across regions demonstrate how challenging achieving universal compliance can be.
2. Embedded Industrial Dynamics
Connectors represent more than physical interfaces—they reflect the technical preferences and industrial ecosystems of their regions. In early automotive supply chains, international brands from the U.S., Europe, and Japan dominated China’s market, bringing their proprietary connector standards. Local automakers had limited negotiation power to replace these imported systems. It wasn’t until later stages of vehicle production that localization efforts began, but even then, achieving true standardization proved elusive.In the EV era, leading connector suppliers have leveraged their early industry foothold to maintain dominance. While connectors are seemingly small components, they are deeply intertwined with industrial power plays, reflecting the challenges of transitioning to a fully localized or standardized supply chain.
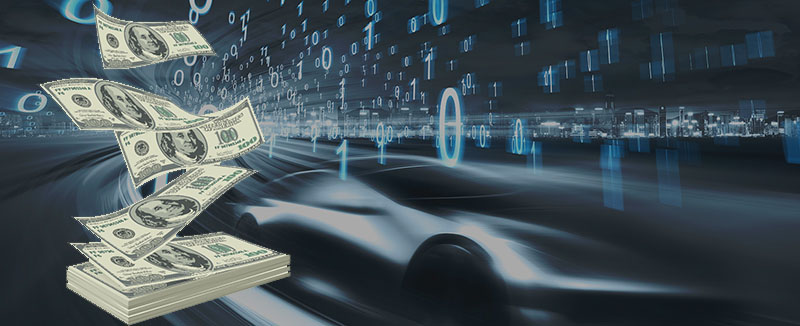
3. Big Profits in Small Components
From a technical standpoint, LV connectors are not highly complex. However, their extensive use across vehicle systems makes them a lucrative market. A single vehicle may use hundreds of different LV interfaces, many of which are custom designs. These connectors contribute to significant hidden costs within EV wiring harnesses, making them a target for cost optimization. Companies like Tesla, BYD, and Huawei have been pushing for connector standardization to streamline costs and support local suppliers. However, the lack of industry consensus and shared incentives continues to impede progress.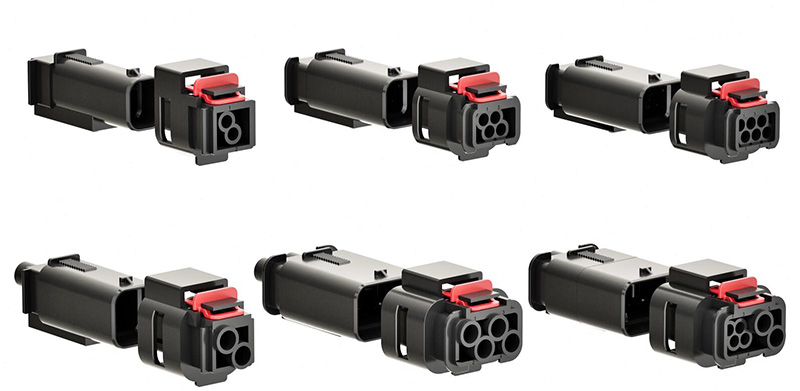
Insights on Tesla’s LVCS
Tesla’s LVCS reflects its commitment to cost efficiency and modular design. Features such as the addition of a Connector Position Assurance (CPA) mechanism, uncommon in LV connectors, enhance reliability. The connector’s diagonal outlet hole layout increases electrical clearance, making it suitable for use across 12V and 48V systems. This design optimizes size efficiency, supporting modularization. The mix of “large” and “small” pin designs accommodates both signal and power needs, a growing requirement in EVs. Additionally, the use of independent wire seals instead of integrated seals improves versatility and performance.The Road Ahead
As the EV industry evolves, the push to unify LV and HV connector interfaces will likely accelerate. The high hidden costs and low technical barriers of LV connectors make them ripe for disruption. However, the final form of standardization remains uncertain. For instance, will we see integrated HV-LV hybrid connectors that reduce size and enhance modularity? Achieving such innovations will require concerted efforts from major automakers to reach consensus and lead industry-wide initiatives.The clock is ticking, and the stakes are high. Tesla’s LVCS is a bold step toward reshaping the industry’s approach to connector standardization. Yet, whether it will become the de facto standard or simply add another layer to the fragmented landscape depends on the industry’s ability to collaborate and innovate.
Message
If you are interested in our products, please fill in the message form below. Our sales representative will contact you within 24 hours.