What Tests do EV High Voltage Wiring Harnesses Need to do?
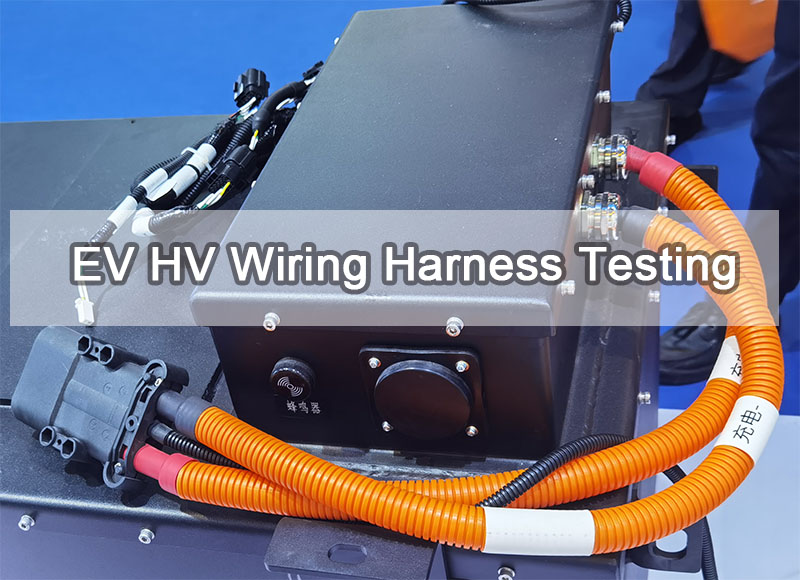
HV harnesses play a crucial role in electric vehicles by ensuring reliable power transmission and safety in high-voltage environments. To guarantee optimal performance, HV wiring harnesses must undergo a series of rigorous tests before deployment. These tests cover electrical performance, mechanical durability, environmental resilience, and safety compliance. Below, we delve into the essential tests required to validate the quality and reliability of EV wire harnesses.
1. Electrical Performance Testing
Ensuring proper electrical performance is critical for the efficiency and safety of HV wiring harnesses. The key electrical tests include:- Insulation Resistance Test: The insulation resistance test is conducted to assess the resistance between any two high-voltage connector terminals within the high-voltage wiring harness assembly, as well as between the shielding and the terminals. This test is essential to validate the safety of the assembly, ensuring that no unintended electrical circuits are formed, which could otherwise pose a risk of electric shock to personnel. To prevent potential test failure due to contamination from prolonged exposure to external factors, the insulation resistance test must be completed within three hours following the initial test cycle on the sample. During the test, an insulation resistance meter is connected between the connector terminals and between the connector terminals and the shielded metal housing. A DC voltage of 500V is applied for a minimum of one minute to measure the insulation resistance across these points. Readings should be recorded once the insulation resistance meter stabilizes. A sample is deemed compliant if it maintains an insulation resistance of at least 100 MΩ when subjected to a DC voltage of 1000V between any two terminals or between a terminal and the shielded metal housing.
- Dielectric Strength (Withstand Voltage) Test: The withstand voltage test is conducted on high-voltage cable assemblies rather than individual high-voltage wires. Its primary purpose is to detect potential insulation defects that may arise during the manufacturing process, which could pose an electric shock hazard to personnel. The test is performed using a high-voltage withstand tester on samples that have been stored at room temperature for at least one hour. In accordance with the test specifications outlined in the "Test Voltage and System Voltage Relationship Table," the required voltage is applied between the connector terminals and between the connector terminals and the insulation layer. The leakage voltage between terminals and between terminals and the insulation layer is measured, and readings are recorded after one minute. Throughout the entire test, the high-voltage wiring harness assembly must not exhibit any insulation breakdown or electrical discharge (arc or spark). Additionally, the leakage current displayed on the withstand voltage testing equipment must not exceed 10mA (GB/T 18488.1).
- Continuity Test: A continuity test ensures that all electrical connections are intact and that there are no open circuits or unexpected resistance levels
- Contact Resistance Test: The comprehensive high-voltage wiring harness testing process includes evaluating the contact resistance within the harness. By measuring the voltage and current at both ends of the connector, the contact resistance value is calculated. This value reflects the connector’s contact performance, as excessive contact resistance may result in unstable signal transmission and energy loss. Guchen Electronic employs automated manufacturing technology for HV wiring harness production, aiming to enhance efficiency while ensuring superior product quality. Precision crimping equipment is utilized to establish reliable connections between wires and connectors, effectively mitigating temperature rise caused by contact resistance. The production process adheres to stringent quality control measures, including wire resistance testing and connector mating/unmating force assessments, to ensure that the high-voltage wiring harness fully meets the specified design standards.
2. Mechanical Performance Testing
HV wiring harnesses are subject to various mechanical stresses in real-world applications. The following tests evaluate their durability:- Tensile Strength Test: This test is conducted to ensure that the wiring harness can withstand the mechanical forces encountered during vehicle assembly and subsequent operation without the cables becoming dislodged from the terminals, which could lead to product failure. The relationship between the conductor cross-sectional area of automotive high-voltage cables and the pull-out force is typically based on industry standards such as ISO 19642, IEC 60228, and LV 215-2. The exact values may vary depending on the manufacturer and specific application requirements. Below is a reference table showing common conductor cross-sections and their minimum pull-out force requirements:
Conductor Cross-Section (mm²) | Minimum Pull-Out Force (N) (Reference) |
2.5 mm² | 200 - 300 |
4 mm² | 300 - 400 |
6 mm² | 400 - 600 |
10 mm² | 600 - 900 |
16 mm² | 900 - 1300 |
25 mm² | 1300 - 1800 |
35 mm² | 1800 - 2500 |
50 mm² | 2500 - 3500 |
70 mm² | 3500 - 5000 |
95 mm² | 5000 - 7000 |
120 mm² | 7000 - 9000 |
This table is for reference only. Specific requirements should be verified according to OEM specifications or technical standards from cable and terminal suppliers. If compliance with ISO, LV, or OEM-specific standards is required, it is recommended to consult the relevant technical documents or conduct actual test validation.
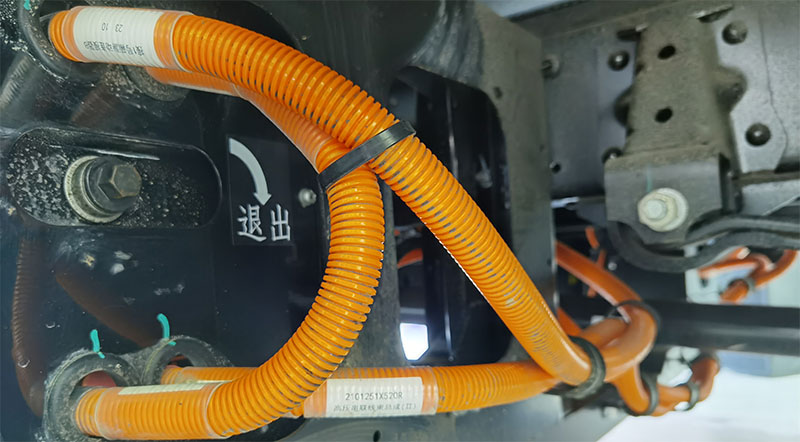
- Vibration Test: Simulates vehicle operating conditions to test whether the harness can withstand prolonged vibration without damage to connections or insulation.
- Insertion and Extraction Cycle Test: Perform a mating and unmating test to evaluate the connection performance of the connector and plug. The connector should securely engage with the plug without any looseness. During the test, observe the metal contacts of the connector to ensure proper conductivity and check for any signs of oxidation, corrosion, or other issues. Taking CCS2 connector for example, the mechanical durability requirement for a CCS2 charging inlet, as defined by IEC 62196-3 and DIN 70121, mandates a minimum of 10,000 mating and unmating cycles to ensure long-term reliability. The inlet must maintain consistent insertion and extraction forces within ergonomic limits, and its locking mechanism should withstand repeated operations without failure. Additionally, it must endure vibration, temperature variations, and environmental exposure, typically meeting an IP54 rating when mated to prevent dust and water ingress.
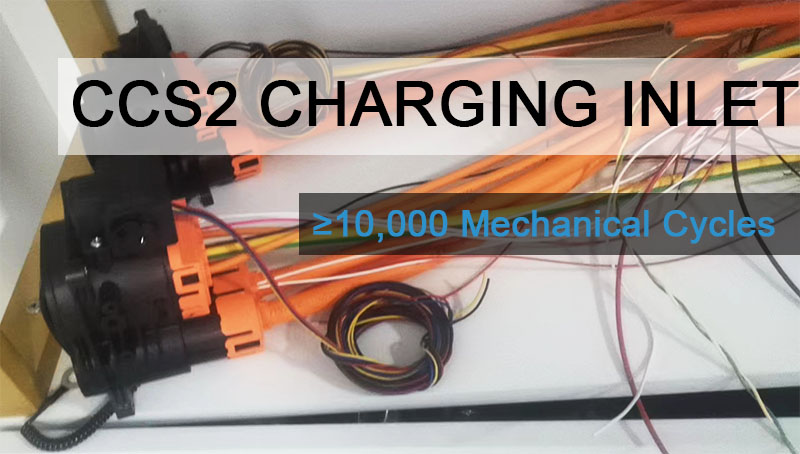
3. Environmental Resilience Testing
To ensure reliability under various environmental conditions, HV wiring harnesses must pass the following tests:- Temperature Cycling Test: The temperature and humidity cycling durability test for high-voltage wiring harnesses is designed to simulate rapid temperature and humidity variations to evaluate the performance of the wiring harness assembly over a specified period. This test assesses the functionality of related components under sudden environmental changes, including failures caused by abrupt temperature and humidity shifts. It also examines material property changes, such as alterations in plastic elasticity and stress, surface damage and deformation, accelerated aging, and degradation or detachment of metal coatings due to corrosion. These changes may affect the electrical and physical properties of the wiring harness assembly.
Upon test completion, the assembly parts should be conditioned at 23±5°C for 1 hour to ensure temperature stabilization. Afterward, visual inspection, insulation resistance, and withstand voltage tests should be conducted. Only if all components meet the required performance criteria can a test qualification report be issued.
- Salt Spray Corrosion Test: Whether for wiring harness accessories such as high voltage connectors, terminals, and clips, or for the entire wiring harness assembly, salt spray testing is an essential part of Design Validation (DV) testing. But what exactly is a salt spray test, and why is it necessary? When a vehicle or truck is in operation, wiring harness connectors may be exposed to water splashed from the tires, especially in winter when roads are treated with salt to accelerate snow melting. To ensure corrosion resistance, these connectors are typically subjected to salt spray testing. This test simulates exposure to corrosive environments (e.g., 96h, 336h, or 480h) to ensure metal components resist rust and degradation. The primary evaluation criterion for the wiring harness salt spray test is the reliability of contact resistance rather than just visual inspection. In many cases, connectors are used together with sealing rings to enhance their resistance to salt spray exposure.
Related reading: The Necessity of Salt Spray Test in EV HV Connectors
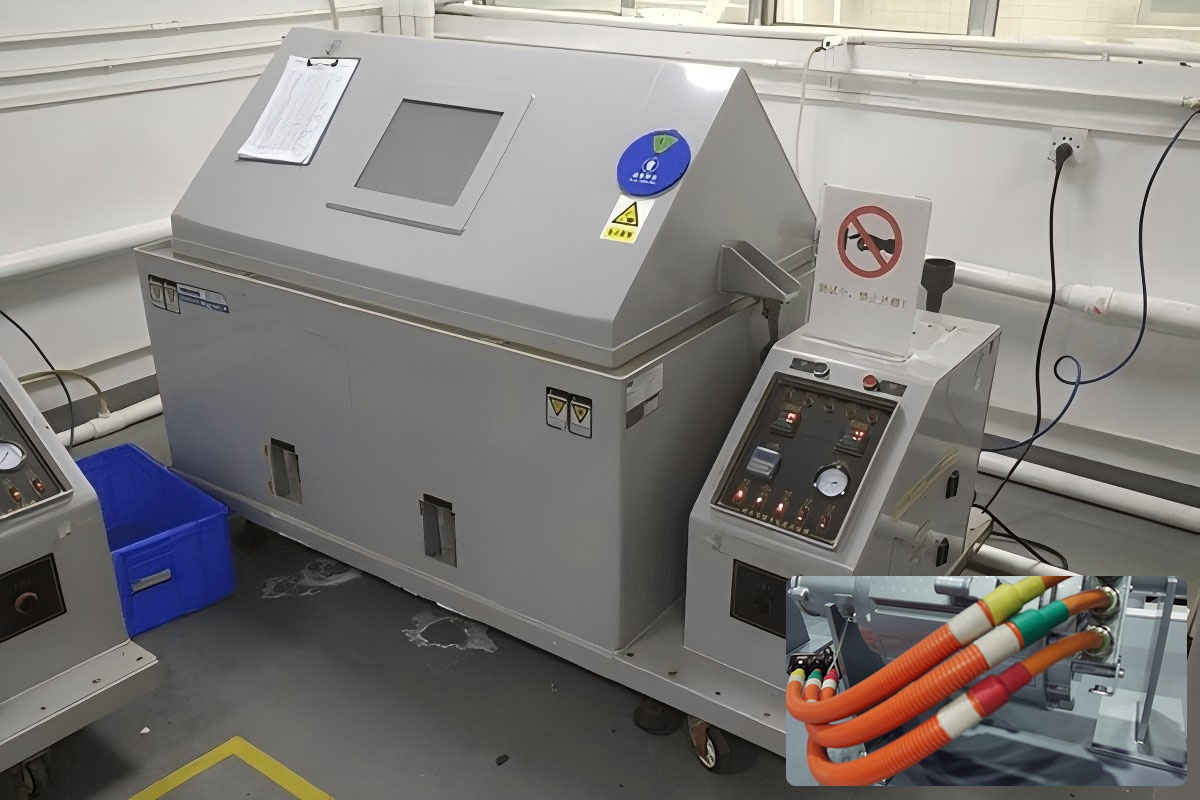
- Chemical Resistance Test: This test is designed to simulate conditions where a vehicle experiences chemical leakage, ensuring that the wiring harness assembly still meets basic functionality and reliability requirements. The test typically requires the vehicle manufacturer to immerse the wiring harness in various solvents used in actual automotive applications (such as transmission fluid, refrigerants, lubricants, engine oil, gasoline, cleaners, brake fluid, etc.). The wiring harness must meet insulation, withstand voltage, and airtightness requirements, allowing for a certain level of deformation.
4. Safety and Protection Testing
Safety is paramount in high-voltage applications. These tests verify the harness’s compliance with stringent safety standards:- IP Testing: It is crucial to ensure their durability and safety under various environmental conditions. The IP rating classifies the level of protection against dust and water ingress, with ratings such as IP67 (dustproof and submersible in water up to 1 meter) or IP69K (resistant to high-pressure, high-temperature water jets). These tests assess the integrity of seals, connectors, and insulation materials, ensuring they can withstand exposure to elements like moisture, dirt, and mechanical stress. EV HV wiring harnesses are tested for environmental factors such as extreme temperatures, UV light, and salt exposure, ensuring long-term performance and safety in harsh conditions, which is essential for vehicle reliability and compliance with industry standards.
- Flame Resistance Test: Evaluates the fire-retardant properties of insulation materials, ensuring compliance with UL94 V-0 or other industry safety standards.
- EMC and Shielding Test: Electromagnetic Compatibility (EMC) encompasses both Electromagnetic Interference (EMI) and Electromagnetic Sensitivity (EMS), referring to the ability of a device or system to operate as intended within its electromagnetic environment without causing unacceptable electromagnetic interference to any other devices in that environment.
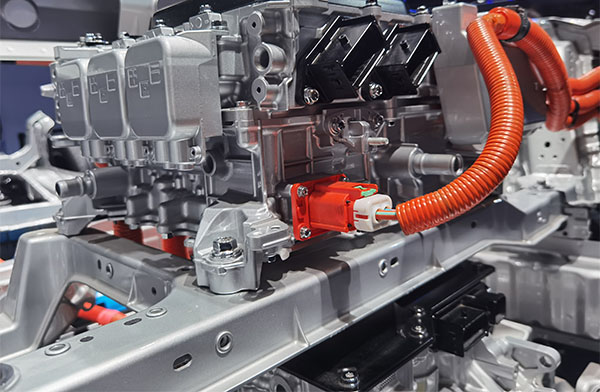
- High-Voltage Interlock (HVIL) Test: It ensures the safety of high-voltage systems by verifying the integrity of the interlock circuit, which prevents accidental exposure to high voltage. The test checks for continuity in the interlock loop, ensuring that any disconnection, damage, or improper assembly of connectors or cables triggers an immediate shutdown of the high-voltage system. Common HVIL tests include resistance measurement, insulation resistance testing, and functional verification under simulated fault conditions. These tests confirm that the interlock system can detect open circuits, short circuits, and improper grounding, ensuring compliance with safety standards such as ISO 6469 and IEC 62196. Proper HVIL implementation is crucial in preventing electric shock hazards, enabling safe maintenance, and ensuring the reliable operation of EV power systems.
Related reading: Everything You Want to Know about High Voltage Interlock Loop
Comprehensive testing of high-voltage vehicle wiring harnesses is essential to ensure their reliability, safety, and longevity. By undergoing rigorous electrical, mechanical, environmental, and safety tests, these critical components can meet industry standards and function reliably in the demanding conditions of electric vehicles. Adhering to international standards such as ISO 19642 and LV 215 further guarantees quality and compliance, providing OEMs and manufacturers with confidence in their HV wiring solutions.
Message
If you are interested in our products, please fill in the message form below. Our sales representative will contact you within 24 hours.